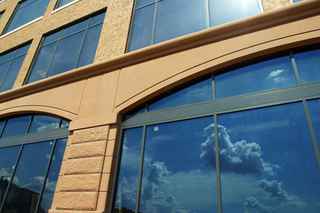

Carbon Footprint.
Two consequential words that have construction industry experts evaluating every material used in the build process. In addition to the challenge of developing high quality, functional and visually appealing buildings that meet industry standards, designers and contractors are now considering the long-term carbon footprint of each project they undertake.
Every material has a carbon footprint, as a result, the design and construction industry is focusing on what we can do to reduce our carbon footprint as a building solution providers. Currently, experts are debating the value of building with energy-saving materials or focusing on reducing a building’s total lifecycle cost, as the best method to decrease the lifelong carbon footprint.
Carbon emissions: manufacturing vs. building operations
The Precast/Prestressed Concrete Institute (PCI) conducted a study of the energy used in a commercial building from cradle-to-grave. This study compared three structural systems (steel vs. cast-in-place vs. precast) as well as three envelope systems (curtainwall vs. brick & steel studs vs. various precast enclosure systems).

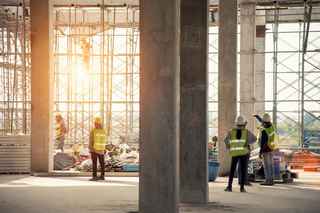

According to the study’s conclusions, “97% of the total primary energy (TPE) and 96% of the global warming potential (GWP) attributed to the building over its lifetime occurs in the operating energy stage.” The facts show that although precast concrete influences the initial carbon footprint, due to the energy use and carbon emissions associated with the manufacturing of cement, it is the operation stage of a building that uses the most energy over the lifetime and precast concrete is a thermally efficient building solution. Specifically, once a building is constructed, the operations (heating, lighting and general building usage) impact the carbon footprint more significantly.
These findings do not mean it is time to give up on finding ways to reduce our carbon footprint during the manufacturing process; it is our duty, not only for the future of the construction industry but for the future of our communities, to provide more sustainable products. At Wells we continue to research ways to reduce the carbon impact.
Insulated precast concrete: an energy saving solution
Utilizing precast insulated wall panels with exposed concrete on the inside results in an energy savings for the building owner. Concrete is one of a few materials that has a thermal mass effect. As people enter the space and equipment turns on, the space heats up. The exposed concrete on the inside of the wall panel absorbs the energy like a battery. When the equipment turns off and people exit the building, it has a tendency to cool down. However, when insulated panels are used, the energy stored in the panel is released back into the space, taking longer for the space to cool down; effectively reducing the heating and cooling requirements of a building.
The long-term impact: reducing a building’s operating energy
Fortunately, since the introduction of Leadership in Energy & Environmental Design (LEED), all stakeholders in the building design team have gotten better at delivering more energy-efficient buildings. Many older buildings while having good bones, have leaky enclosure systems.
As an industry we continue to develop methods to reduce the 4% carbon contributed from the manufacturing processes, while also focusing on ways to reduce the 96% contributed from the building’s operating energy. Enhancements in this arena, can make a bigger and more noticeable difference sooner.
One step building owners can take to harness long-term operations savings is to ensure the building is performing optimally. Utilizing preventative maintenance on the building's exterior, such as Wells sealants and restoration services, and upgrading to effective heating and cooling systems can lead to further reducing energy usage and your carbon footprint.
Interested in learning more about Net Zero Building with Carbon Fiber Reinforced Precast while earning continuing education credits? Join this self-paced online continuing education course provided by our partner, AltusGroup.