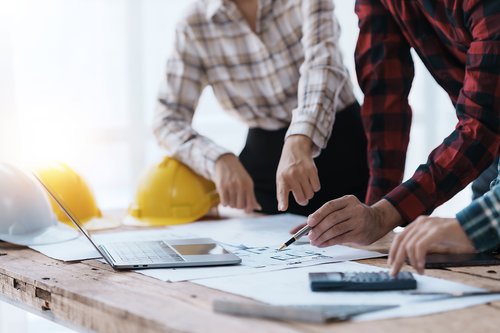
When designing with prefabrication, often a small tweak to a structure’s design can reap huge benefits down the road. Engaging a prefabricator during preconstruction is critically important, as they can help guide design decisions with an eye for efficiency and value-engineering.
At project onset, prefabricators will evaluate the project and suggest cost-saving alternatives to ensure that the design is compatible with manufacturing equipment and methodologies – long before changes become costly. In the architecture world, no two projects are alike. An architect may start a project considering precast as one of several building options, or it may not be in the consideration set at all. In some instances, the designs are already completed, but due to price, schedule or building material supply chain availability, significant design changes are needed to make a project come to life.
In each case, prefabrication specialists bring different ideas to the table, often providing an itemized cost analysis that depicts the potential savings of a variety of precast alternatives.
Increasingly, prefabricators are becoming “one-stop-shops,” of sorts, by taking on larger roles in the designs of structures. An architect might merely provide the basic dimensions of a parking garage, for example, then hand the rest of the design over to the prefabricator. In the process, the prefabricator is taking work off their plate. Wells’ in-house engineering department, for example, often supports partners with this effort, developing shop drawings for entire structures or individual precast components.
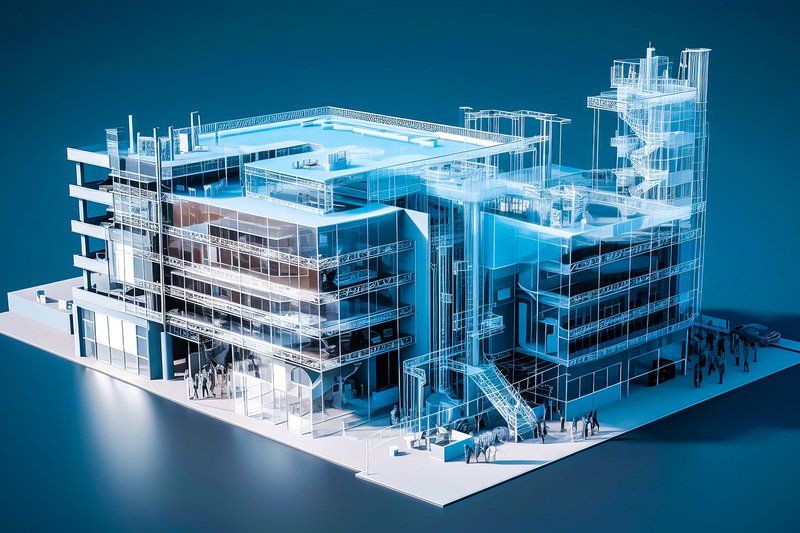
Design-Assist Tackles Problems Early
For larger projects, design-assist is the best way to ensure that the benefits of precast are maximized. Design-assist is an in-depth process, whereby the prefabricator’s engineer and modeler “get into the weeds” of the design with the entire project team.
That often requires weekly meetings between the prefabricator’s engineer, the engineer of record and the architect. During those meetings, the team collaboratively shares and works through the model, locating openings and penetrations with the intent of reaching a consensus for the most cost- and time-efficient building solution – while maintaining the original design intent.
Along the way, they’ll look for ways to create repetition in the design. That can lead to significant cost savings, such as casting similar sized panels with less forms, requiring less manufacturing labor and lowering material costs, as well as create engineering efficiencies as panels with similar design are less time consuming for design and engineering to work through.
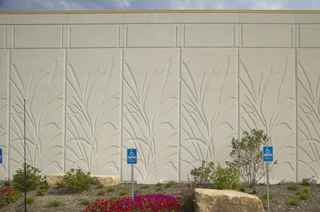

Little Six Casino; Prior Lake, MN
Nevertheless, just how much repetition can be achieved depends largely upon the original design and the ability to make changes. To assist design teams in decision making, Wells often brings designers to our manufacturing facilities to show them our processes, as well as examples of forms and production beds to show the importance of maximizing the efficiency of the production cycle.
While design-assist meetings can be executed in person, they’re often done virtually to accommodate design teams located in other states or regions. In the process, the prefabricator will create and share the design model with the team, then as a team they’ll discuss panel design, finishes and connections (see our Design Handbook).
There are other benefits derived from the preconstruction process. By the time the project is underway, the groundwork for collaboration and coordination has already been established, making for a smoother transition to construction. With a design-assist approach, the design schedule can be expedited by starting manufacturing of the materials simultaneously while the sitework begins and the foundations are set.
Ultimately, a project team who initiates the help of the prefabricator during preliminary designs will reap rewards of both time and money. That’s when the project has the most flexibility and the most savings can be realized.
Other Resources:
More information about Wells’ preconstruction services.
Check out Wells’ design handbook resource for architects and engineers.
This article was authored by Reid Mordhorst and Alex Wiltfang.