The electric vehicle boom is here, and while EVs may resemble traditional gas-powered cars, their design fundamentally alters their attributes. As EVs rapidly become a mainstay on our roads, understanding their impact on parking structures is more crucial than ever.

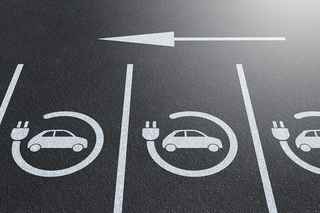

Before we can dig into how EV loads will affect parking garages, it’s important to understand the growing adoption of EVs. The current expansion of EVs within the United States and the world is rooted in concerns for climate change fueled by concerned citizens and accelerated by the federal government. The increasing market-driven competition has also begun to make electric vehicles a competitive option; with the adoption of EVs expected to grow substantially over the next several decades. This raises important questions about the ability of the nation’s current infrastructure to handle an increase in EV traffic. More specifically to the precast industry, how does this impact parking structures now and in the future?

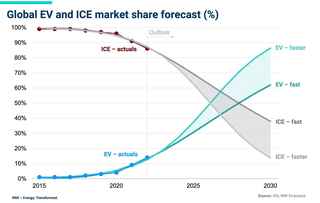
Source: Rocky Mountain Institute: https://rmi.org/the-ev-revolution-in-five-charts-and-not-too-many-numbers/
Differences Between EVs and ICEs
EVs differ not only in weight but also in weight distribution compared to their internal combustion engine (ICE) counterparts, largely due to the high density and positioning of the batteries. A typical EV battery can be extremely heavy, weighing between 1000lbs and 2000lbs! ICE vehicles typically have a front-heavy center of gravity due to the engine placement in the front of the vehicle. Batteries for an EV are typically placed below the cabin between the wheels, resulting in a more balanced center of gravity.

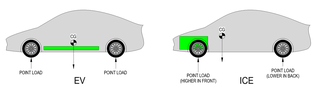

Incentives and Driving Forces for the Future of EVs
To predict the future of EVs, it’s necessary to understand current conditions and the incentives and driving forces shaping the technology.
Currently, consumers are demanding increased range, often reported as “range anxiety”. This demand pushes EV manufacturers to increase battery size to achieve longer ranges. However, increasing battery sizes lead to diminishing returns. A larger battery reduces efficiency because it requires more energy to move the vehicle. Efficiency is critical with EV batteries since they’re significantly less energy-dense than gasoline., which has about 12,700Wh/kg compared to approximately 265Wh/kg for EV batteries. To compete with gasoline, EVs need to prioritize energy efficiency, which means striving for lighter batteries while balancing the consumer demands with technological capabilities.

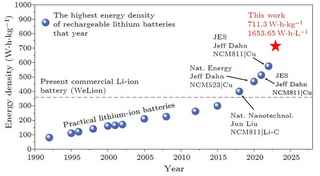
Source: Physics World: https://physicsworld.com/a/lithium-ion-batteries-break-energy-density-record/
Battery energy densities used in EVs have increased in recent years and is expected to continue. In the short term, consumers may drive EV weight upwards as they demand more range, with current range demand somewhere between 300 and 400 miles per charge. Tesla dominates the EV market, accounting for more than 50% of EV vehicles on the road today. The current best-selling EV is the Tesla Model Y with 31.9% of vehicles sold in Q4 2023 with the Model 3 following closely at 17.6%. These two vehicles are already close to satisfying range requirements of consumers. As electric vehicles achieve ranges of 300-400 miles, it is not likely that they will get heavier. Battery energy densities are expected to increase, resulting in either additional range and/or less weight. For this reason, EV weights are likely to decrease over the long term.
The average weight of a new vehicle sold in the U.S. in 2022 was 4094lbs. Compare this to the 2024 models of the top 10 sold vehicles in the U.S.; the weight of the Model Y (4,154lbs) and Model 3 (3,891lbs) are par for the course. Generally, an electric vehicle is heavier than a car and closer in weight to an SUV or a truck. The Tesla Model 3 Long Range, for example, is 20% heavier than a Toyota Camry SE.
Top 10 Best-Selling Vehicles in U.S. in 2024
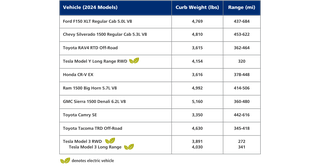
Source: Edmunds: https://www.edmunds.com/most-popular-cars/
Design Criteria of Parking Structures: Distributed Versus Point Loads
So, what does this all mean for the future of parking structures? To evaluate the impact of heavier EVs on parking garages, we need to first understand the design criteria. While there are many considerations for the design of precast parking garages, the criteria can be broken down into distributed loads and point loads. A distributed load represents the weight of multiple vehicles over a larger area whereas a point load represents a single concentrated load from something like a wheel or a jack.
Load and Resistance Factor Design (LRFD) is used for the design of modern parking garages. Load factors are a multiplier on service loads that represent the maximum load that could be expected and are meant to account for the unpredictability of loads. The higher the factor, the less predictability in loading. Resistance factors are multipliers meant to account for variations in material properties to reduce the assumed capacity. Below is the typical controlling load combination for a parking garage.
U = 1.2D + 1.6L +0.5S
U = Required Strength
D = Dead Load (the structure, permanent fixtures, etc.)
L = Live Load (vehicles, people, etc.)
S = Snow
ASCE 7 is the code that dictates the required loading for parking garages and other buildings in the US. The prescribed loads for a parking garage are a distributed load of 40psf (pounds per square foot) and point load of 3,000lbs. The commentary within ASCE 7-16 provides critical insight into the origins of these loads. Section C4.7.4 explains a load survey conducted in 2001 at nine different commercial parking garages in four cities (Wen and Yeo 2001). This study found that typical distributed loads were conservatively estimated at 34.8psf. In addition, the study found a low coefficient of variation of 5% compared to 20% - 30% seen with typical live loads. This means that both the 40psf design load as well as the 1.6 load factor are conservative for today’s parking garages. The average vehicle weight in 2001 is comparable to the average weight of today’s vehicles. Assuming a conversion of an ICE vehicle to an EV is approximately 20% heavier (based off the earlier comparison between a Tesla Model 3 and a Toyota Camry SE), that would change the 34.8psf load to around 42psf, which would not be a significant concern for today’s parking garages.
Section C4.7.4 of the ASCE 7-16 code attributes the 3,000 lb point load requirement to a 10,000 lb vehicle impacting a 4.5” x 4.5” area representing a load caused by a jack in changing tires. The heaviest EV on the market is the 2024 GMC Hummer coming in at a curb weight of 9,063lbs! Despite the heaviest EV on the market, current garage design requirements are adequate.
Parking spaces vary but are typically 9ft x 18ft with a 16ft to 20ft drive lane. Imagine a worst-case scenario, dubbed an “EV Hummer Party”, where each parking spot was filled with a 9,063 lb Hummer. The resulting distributed load would be only 38.7psf. Considering the load factor of 1.6 previously discussed, there would be no serious concern for any electric vehicles under 10,000 lbs.

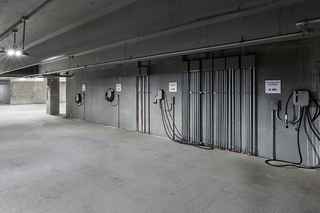
Existing Parking Structures are Likely Sufficient for Future EV Loads
With all the information available today, it is unlikely that increased adoption of EVs in the future will cause any significant cause for concern regarding parking garage performance. Provided an existing parking garage was designed and produced in conformance with building codes at the time, they are already designed to take the expected future EV loading. It is possible that EVs may get slightly heavier than they are today to address consumers’ range anxiety, but exponential progress of battery technology will likely result in EVs eventually becoming lighter.
A Warning about Deficiencies
There is one caveat – any increase in loading could uncover pre-existing structural deficiencies or code deviations. Should a structure not meet the minimum code requirements for loading at the time they were built, any additional loads could result in overloading. This is true for any structure but deserves mention in situations where loading is expected to increase. Point loading and connections are particularly susceptible since horizontal members can readily redistribute loading to other structural members.
Nevertheless, as the EV industry evolves, several variables could change the design dynamic. The debate over load capacity will likely continue as EV battery technology advances and adoption rates continue to evolve.
Note: Calculations within this article are estimated. Make sure to consult a Wells parking garage expert to ensure structure design meets code requirements and structural integrity minimums.
Related parking resources.
View more Wells parking projects.