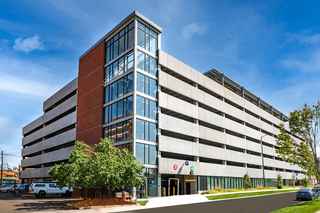
Parking Garages that Stand the Test of Time
Parking structures are unique building types – combining the challenges of a bridge and building into one – supporting all the durability and exposure of a bridge with cars tracking in dirt and salt while being exposed to the elements, and in cold climates freezing and thawing. When it comes to the parking structure façade, attention needs to be given to water proofing to protect from the effects of thermal change.
Total precast parking structures are the most prevalent parking structure building system used in the U.S., and for good reason. Manufactured off-site, the total precast parking structure combines quality, durability and reliability at a competitive cost. A true differentiation is the accelerated speed of construction that can carve months off the construction schedule and the ability to be constructed in all types of weather. So how can you get the most out of your precast parking structure investment and have it stand the test of time?
How to Optimize Your Precast Parking Garage Investment
Step 1: Design the Parking Structure to Last
Involving a seasoned precast team throughout the project from pre-construction through completion, supports upfront design assist work, engineering and fine-tuning of the plan and modeling for each parking structure project. These teams help design an efficient structure to fit the site, while bringing a unique understanding of code requirements, ADA accessibility, slope limitations, drainage and more, establishing a plan and adding value to the design process.
The parking structure is often the first and last impression for visitor experience. When integrated in neighborhoods and campuses, the desire is to have a parking façade that no longer looks like parking, so special attention is being given to the architectural design. Leveraging a wide array of architectural finish options and techniques helps parking structures integrate into the surrounding community.

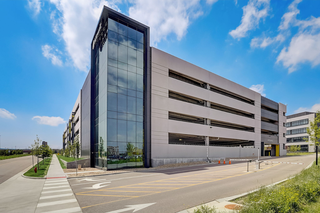

A structure’s longevity is an undeniably important part of the design calculus. Fortunately, there are some effective steps that structure owners can take to ensure that future maintenance doesn’t go from minimal to major.
Step 2: Protect the Parking Structure
Water is the primary enemy for most building materials. Water infiltration can lay the groundwork for concrete to break and spall, and subsequently corrode the reinforcing steel, leading to degradation of the parking structure.
Sealants are the first line of defense. A typical total precast garage will often contain several 10- to 15-foot-wide spans of concrete, with ¾- to 1-inch joints, and the sealant provides a vital barrier that blocks water intrusion and channels it to a catch basin or drain area.
Architects and structural engineers have begun to give sealants more attention, as they focus on providing the best lifetime value for their clients. In recent months, a new hybrid form of sealant has caught our team’s eye. Essentially, the product is a blend of silicone and urethane, resulting in a sealant product that is less costly than silicone but with a much-improved lifespan.
In fact, the hybrid’s warranty can reach 15-20 years, as opposed to the traditional 5-8 years for standard urethane. Perhaps more encouraging, a new traffic grade hybrid has been developed that is specifically tailored for parking structure applications. The product can achieve a hardness upon curing that holds up well under traffic, providing it with the durability it needs, along with greater UV stability and longevity.
Step 3: Parking Garage Maintenance
Still, over time, any structure can begin to show signs of wear. Once a building system begins to deteriorate, the process will continue until repairs are made. A quarter-sized hole will only get larger, spall and crack as it’s put through the typical freeze and thaw of a northern U.S. winter. With annual inspections, total precast parking structures can last longer and for lower cost without ever needing an expensive overhaul.
A system of regular maintenance – as opposed to waiting for significant damage to occur – can significantly lower the cost and increase the longevity of the overall structure. In fact, the PCI Maintenance Manual recommends a semi-annual inspection, as well as offers a full maintenance checklist. When identified early, issues can be fixed for minimal cost.

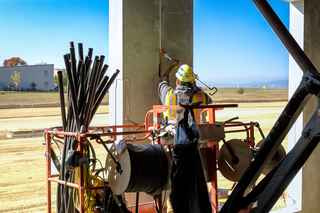

Minimize Lifetime Costs with a Maintenance Plan
At Wells, after a project is complete, our Sealants and Restoration team proactively works with owners to implement a long-term maintenance plan for their parking structures, thereby extending structure life and minimizing lifetime maintenance costs.
Ultimately, total precast or prefabricated parking structures that are maintained through a regular system of inspection, remain the most cost-effective, long-term parking structure solution that is continuing to stand the test of time.
Learn more about Wells Parking Structure Maintenance Program | Submit Your Project Inquiry