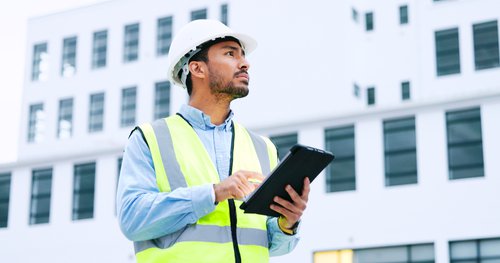
Buildings designed with precast are proving they can withstand the rigors of time. When built properly and maintained through regular inspections, this building solution is essentially an ageless one.
Much of the reason can be traced to the way precast is created. During manufacturing, panels and beams are typically constructed using high-strength concrete, measured in its pounds per square inch (psi) compressive strength. The reason? For efficient use of manufacturing space, the concrete must quickly reach a minimum design strength of 3,500 psi to enable the panels to be stripped from the forms. The concrete eventually tops out as high as 10,000 psi, creating a highly durable and long-lasting product.
The pre-tensioning of the panels plays another role. When constructing precast insulated wall panels, for example, pre-tensioning strands are tensioned to 65 to 70 percent of their ultimate strength before the concrete is poured. Once the strands are cut, the panels are placed in compression.
That has immeasurable benefits in terms of longevity. As hairline cracks develop – as they do in any concrete product – the compression keeps them from growing and expanding, essentially providing another layer of protection and increasing the longevity of the panel.
For these and other reasons – like how precast is also inherently non-combustible and holds up well in high-wind environments – the typical total life cycle cost of a precast structure is lower than most other materials. Parking structures made from precast building materials at the Mall of America in Minneapolis, built in the 1990s, look much as they did when they left the manufacturing facility some 35 years ago.
This comes with some other, perhaps unintended benefits. Since precast experiences little to no deterioration, well-maintained buildings and structures can be easily reconfigured or repurposed decades after their construction. There are countless examples – a warehouse building in Brooklyn Park, Minn., recently underwent its third reconfiguration, and precast components from a 1970s-era single-level parking structure at the Minneapolis-St. Paul International Airport were recently re-purposed as a warehouse roof.
Many precast structures, in fact, are now being designed for this. Owners recognize that when structures are created in a manner that enables future adaptations, reconfigurations or expansions, they add value and marketability.
Annual inspections provide longevity boost.
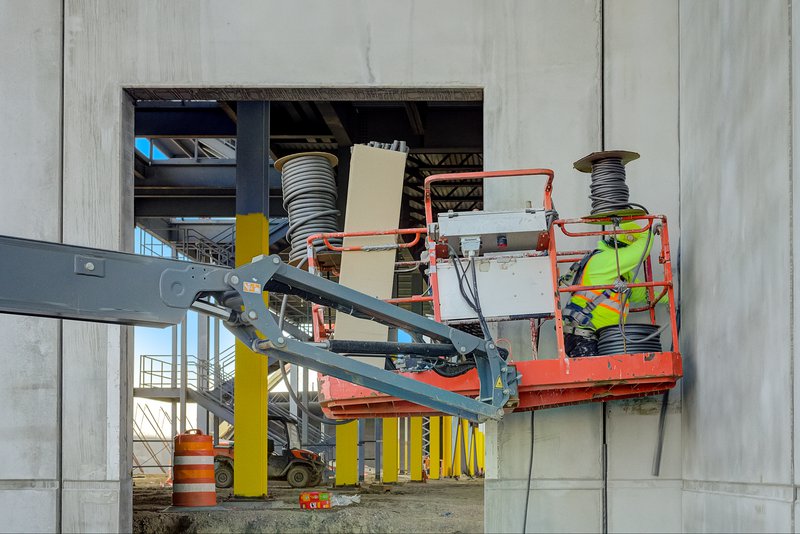
Of course, all structures, regardless of building materials used, require some attention over their lifespans. While many can last decades without a regular inspection program, the potential for costly damage is too high to ignore. In a parking garage, for example, while sealant advancements are extending the life of caulk joints, if not maintained they can deteriorate and crack, causing water leaks and ever-expanding damage. Depending on regional climate, this could lead to freeze-thaw conditions and potentially damage the structure.
With annual or semi-annual inspections (per PCI Maintenance Manual guidelines) precast structures can last longer and for lower cost, without ever needing an expensive overhaul. A simple and inexpensive process that plays a critical role in lengthening its lifespan.
The proper application and maintenance of sealants is a first line of defense, as it provides a vital barrier that blocks water intrusion. Recognizing a need in that arena, Wells launched its own Sealants and Restoration team for the purpose of installing, restoring, re-purposing or extending the life of existing structures. From the outset of every project, they offer added protection for builders, owners and management, with transformative solutions and maintenance strategies to ensure a long and dependable life for any structure.
It's easy to understand why precast – and increasingly total precast – designs are gaining a foothold in many market sectors. The ease of construction, design flexibility and longevity make it an attractive option for many owners, as they seek to do more with less and create structures that will be here well into the future.
Learn more about Wells Sealants & Restoration | Submit Your Project Inquiry
This article was authored by Gary Pooley and Mike Troje.