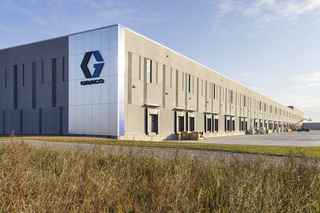

Precast as a modern solution for warehouses.
As the demand for warehouse and distribution centers continues to soar, so too do the challenges of traditional construction methods. Rising steel costs and unpredictable weather conditions can significantly impact project timelines and budgets. A compelling alternative that's gaining traction is a total precast warehouse, where the entire structure, including the roof, is precast.
Why Choose Precast Concrete?
Accelerated Construction Schedules
- Optimized Design and Production: Precast components are designed and manufactured simultaneously, streamlining the construction process.
- Weather-Independent Production: Unlike traditional construction, precast elements are produced indoors, regardless of weather conditions.
- Reduced On-Site Labor: Precast components arrive at the construction site ready to be installed, minimizing on-site labor and accelerating the project timeline.
Cost-Effective Solution
- Material Cost Savings: Precast concrete offers a cost-effective alternative to traditional steel-framed structures, especially in regions with fluctuating steel prices.
- Reduced Labor Costs: The modular nature of precast construction reduces labor costs and project overhead.
- Long-Term Durability: Precast concrete is highly durable and requires minimal maintenance, resulting in long-term cost savings.
Enhanced Building Performance
- Superior Insulation: Precast concrete walls can be integrated with continuous insulation, improving energy efficiency and reducing operational costs.
- Fire Resistance: Precast concrete offers excellent fire resistance, protecting your building and its contents.
- Soundproofing: Precast concrete walls provide superior soundproofing, creating a quieter and more productive work environment.
Design Flexibility
- Customizable Designs: Precast concrete offers a wide range of design possibilities, allowing you to create unique and functional warehouse spaces.
- Adaptability: Precast components can be easily modified to accommodate future expansion or changes in operational needs.
Improved Site Safety
- Controlled Manufacturing Environment: Precast components are manufactured in a controlled environment, reducing safety risks associated with on-site construction.
- Faster Construction: Accelerated construction timelines minimize exposure to potential hazards.
By choosing precast concrete for your next warehouse or distribution center project, you can benefit from faster construction, cost savings, and superior building performance.
Ready to learn more? Contact Wells today to discuss your specific project needs and explore the advantages of prefabricated construction.

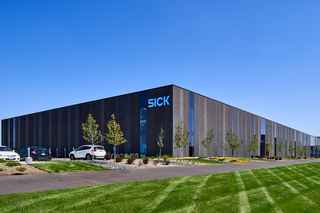