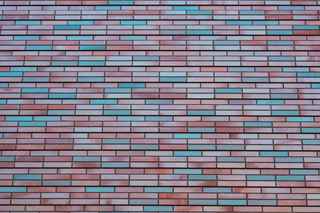

Since the mid-1960s, the combination of precast concrete and masonry has offered the best of both worlds—the efficiency and durability of precast concrete with the timeless beauty of hand-laid masonry. However, when comparing insulated precast concrete wall panels with a thin-brick exterior to traditional masonry cavity walls, precast offers several distinct advantages.
Advantages of Precast Concrete Over Traditional Masonry
1. Efficiency
Precast concrete wall panels eliminate the need for large on-site masonry crews, significantly reducing labor costs and minimizing scheduling delays caused by time-consuming fieldwork.
2. Speed and Planning
Precast wall panels can be manufactured simultaneously with site preparation and foundation work. This just-in-time production strategy enables faster wall system completion, allowing weeks-long masonry work to be finished in just days with a precast installation crew.
3. Controlled Conditions
Unlike traditional masonry, which is weather-dependent, precast concrete is manufactured in a controlled indoor environment. This eliminates delays due to adverse weather and ensures consistent quality.
4. Superior Insulation
Precast insulated concrete walls provide a continuous thermal envelope, unlike masonry cavity walls, which often contain thermal breaks and air gaps that compromise insulation performance.

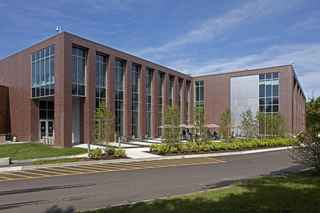
Boston Scientific, in Maple Grove, MN, utilizes a thin brick exterior

Thin Brick Precast Wall Panels
Offsite Construction Process
Although insulated precast concrete wall panels with a thin-brick exterior may appear similar to masonry cavity walls, their manufacturing and performance are vastly different. Precast panels are built in a factory setting using a structured assembly-line process with rigorous quality control measures.
Step 1: Thin Brick Placement
Thin-brick material is laid into a plastic liner within long casting beds, ensuring precise alignment and uniform mortar joints.
Step 2: Reinforcement and First Concrete Layer
Reinforcement is added, followed by a 3" to 4" layer of high-strength concrete, encasing the thin-brick and forming a durable exterior shell.
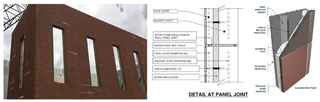

Step 3: Insulation Application
A 3" to 4" layer of board insulation is placed over the concrete, secured with non-conductive fiber ties that prevent thermal bridging.
Step 4: Final Reinforcement and Concrete Pour
A second reinforcing layer is added, and a 4" to 6" concrete backup structural layer is poured. The steam-curing process ensures rapid strength development, allowing panels to be stripped, cleaned, and transported within hours.
Installation of Thin Brick Precast Wall Panels
Once delivered to the job site, precast panels are installed immediately using cranes. A crew of six to ten workers can install 12 to 14 panels per day. After installation, panel joints are sealed with foam insulation and caulking, creating a high-performance, watertight system with continuous insulation.

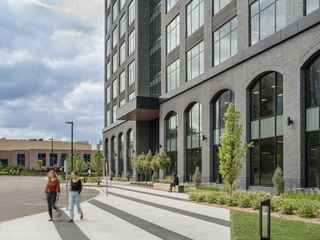
10 West End, in St. Louis Park, MN, showcases precast thin brick arches

Traditional Masonry Cavity Walls
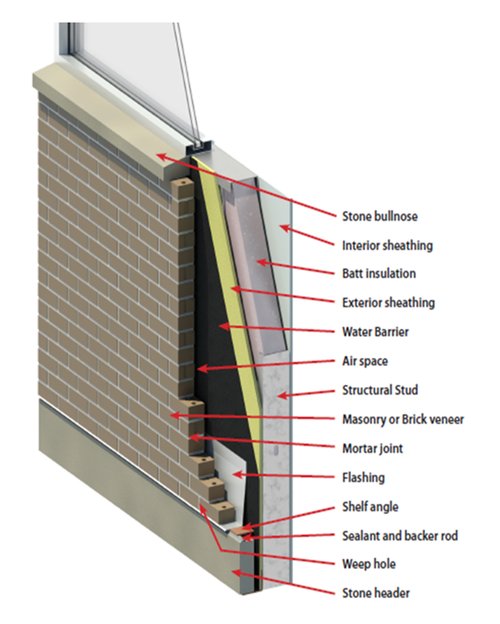
Masonry cavity walls are constructed on-site using an exterior brick facade and an interior masonry block wall. These two layers are separated by insulation and an air gap, with metal ties connecting them for structural stability. This method allows for design flexibility and the traditional aesthetics of hand-laid masonry.
However, metal ties that puncture the insulation can create thermal breaks that reduce energy efficiency. Additionally, the cavity air space can accumulate moisture, requiring careful detailing with flashing, weeping, and venting systems to prevent water infiltration and maintain long-term performance.
Energy Efficiency in Building Design
With modern building codes increasingly prioritizing energy efficiency and net-zero energy goals, traditional cavity wall construction is becoming less viable. Insulated precast concrete wall panels offer a superior solution, providing excellent energy performance, faster construction schedules, and the elegance of traditional masonry—all while enhancing long-term sustainability.