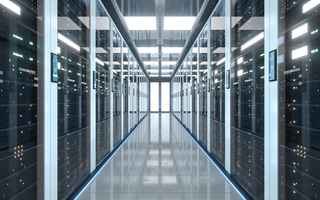

The data center market has been and is still expanding dramatically. The increase of the Internet and extensive use of desktop systems, smartphones, social media, wearable devices, and connected devices is propelling the demand in the global data center construction market. Leading business organizations are embracing innovative technologies such as big data and cloud services to stay competitive in the global market and boost revenues. The global data center construction market is witnessing a jump in growth due to the emergence of augmented reality (AR), virtual reality (VR), and cloud-based technologies, along with a high deployment of smartphones in developing economies.
A market report from Mordor Intelligence shows that the data center construction market was valued at USD 20.11 billion in 2019, and is expected to reach a value of USD 32.50 billion by 2025, registering a CAGR (Compound Annual Growth Rate) of 8.34% over the forecast period of 2020–2025. By the end of 2018, 550-megawatt data centers were under construction across Europe, North America, Middle East, and APAC, with the North American markets accounting for about 44% of the total.
Yet another, and much simpler, reason the global market is growing is the immense amount of data consumed every day. Rising demand for energy-efficient data centers is increasing the need for low-heat-emanating building materials. Reuse of waste and evaporative cooling are some of the green strategies being adopted in order to support the emergence of energy-efficient data centers.
In mission-critical infrastructures, all components must operate each and every day, without exception or incident. Speed to market, increased efficiency, sustainability and reliability are crucial. Precast concrete structural and envelope systems meet the highly specialized demands of mission-critical data centers by providing cost-effective open spans, passive fire resistance, and durable, high-efficiency, low-maintenance building envelopes.

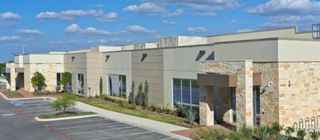

As the need for data centers grows, the demand for durable, resilient and insulating exterior walls will grow, too. To meet these design needs, total precast building systems have become the system of choice.
- Strength and Resilience: The renowned strength of precast concrete offers unparalleled resistance to fires, natural disasters, insects and mold. Like no other building material, its resistance to rain, wind damage, earthquakes, termites and decay provides lower maintenance and insurance costs. It can also withstand many winters of freeze-thaw cycles better than other building materials.
- Quality and Speed: Factory-fabricated precast panels are manufactured in a controlled environment with rigorous quality control procedures. Precast panels are made in advance and stored, then brought to the jobsite as soon as erection is feasible. This innovative process compresses project schedules, reduces safety concerns, reduces site disruption and reduces overall project costs by requiring fewer trades for construction and fewer people on-site.
- Energy Efficiency: Data centers require significant HVAC capacity to offset the heat generated by the servers, and the sophisticated systems draw large amounts of energy off the grid. Using precast wall panels with continuous insulation can provide R-values of R-20 or more depending on insulation thickness. Costs associated with heating and cooling can be greatly reduced through concrete’s thermal mass benefits. Reduced peak heating and cooling loads can be achieved because concrete reacts slowly to changes in outside temperature.
The goal of a data center is to keep your information safe and secure. Stringent design requirements consider conditions like hurricanes, fire and other forces of man or nature, and our data center products and solutions provide the ultimate in quality, security and safety. Precast concrete, a highly efficient, practical method of concrete construction makes beautiful data centers possible at a cost that rivals even the most utilitarian industrial building. Understanding some of the benefits of precast concrete will assist designers in evaluating the impact of precast concrete on the environment and the building operation.

Design Challenges | Precast Concrete Solutions |
Create specialized spaces for technical processes and equipment. | Precast concrete components can provide the design flexibility and durability needed to provide added HVAC infrastructure, such as larger clearances in shafts, ceiling spaces, plenums, and chases. They can also help meet needs for floors that are accessible. |
Eliminate vibration that could disrupt sensitive experiments. | Precast concrete’s solid mass and structural support for HVAC and other equipment helps ensure that rooms are not impacted by equipment operating elsewhere. |
Design clean rooms that can remain completely free of dust or particles. | Treatments are available to help precast concrete panels ensure that no outside particles interfere with clean-room research. Precast concrete systems can also provide the large open-span spaces that are required for mechanical equipment to filter air, while providing the vibration resistance needed to ensure that sensitive equipment performs properly. The panels can be rubbed with mortar after casting to fill every pin-sized air void before the final finish is applied, ensuring a solid surface with no microscopic ledges to hold contaminants. They can also be treated to fight bacteria growth and resist mildew. |
Provide a durable interior environment that can be kept clean and withstand harsh chemical treatments. | Precast concrete insulated sandwich wall panels provide a durable, finished interior that can withstand cleaning, as well as high humidity that would corrode metal. They can also be designed to achieve a maximum four-hour fire rating to help contain accidents. |
Provide a secure enclosure that protects research and prevents disruptions. | Precast concrete’s high durability and impenetrability ensures no security breaches through wall penetrations. Inherently noncombustible composition, along with compartmentalization designs, contains fire to specific areas and allows for detection, evacuation, and suppression. The material also provides strong resistance to harsh weather. |
Minimize operating costs to keep budgets under control. | Insulated sandwich wall panels offer an energy-efficient façade that aids in controlling heating and cooling costs. A total precast concrete system expedites construction, minimizes the number of component pieces by combining structural and architectural attributes into a single piece, and offers single-source responsibility from the precaster. |
Meet the area’s seismic requirements. | Precast concrete systems, using proven connection technology, allow precast concrete components to be used in all seismic zones. |
Expedite construction to provide faster return on investment. | Component casting begins when the shop drawings are complete, ensuring that erection begins as soon as the site is prepared. Year-round, all-weather construction ensures that schedules are met. |

Note additional resources:
- A Case For Precast: A Smart Solution For Designing Data Centers
- Global Data Center Construction Market Outlook
- Denver an Emerging Market for Data Centers, says Study
- Denver Poised for Data Center Industry Growth
- What’s ahead for data center design and construction in 2019 and beyond
- Report: By 2025, Modular Data Center Market To See 23% Growth