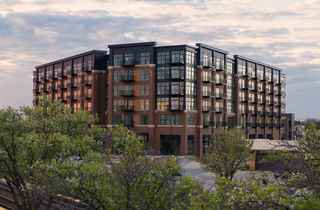

Maple Street Lofts - Mt. Prospect, IL. Read the project profile here.

Precast podiums are no newcomer to the construction landscape. They’ve been around for some 40 years, often serving an indispensable purpose as both parking garages and foundational support for fast-tracked apartments, hotels, condominiums, government, offices and other commercial buildings.
What is podium construction?
Also known as pedestal or platform construction, podium construction is a type of building characterized by horizontal divisions between an upper tower and lower “podium.” Usually, the podium is constructed of prefabricated concrete and then topped by multiple wood, concrete, or metal-framed stories above.
Concrete Podium Construction
Precast concrete podiums are perfect for ground-floor retail and commercial spaces, as well as for incorporating gardens, outdoor pools, and terraces or extra parking spaces. Additionally, the precast components used in podium construction offer durability and strength in the whole structure for high-demanding applications. This makes the podium-style building very strong and sturdy.
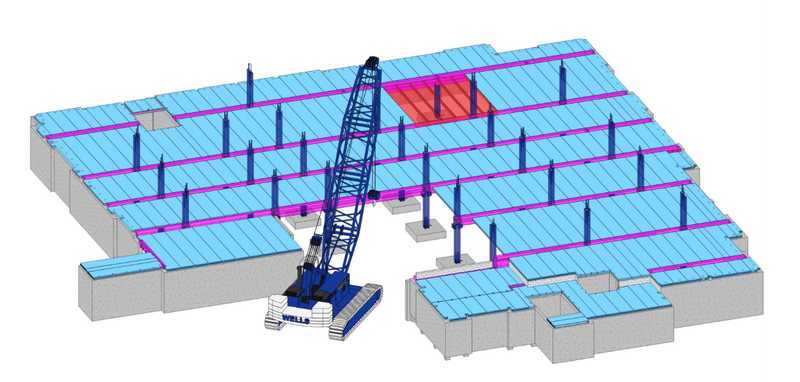
When erecting multiple levels for a podium design, crane access is carefully planned to support piece weight and site logistics.
The Rise of Concrete Podiums in Building Design
The 2015 IBC code change made a significant change to podium use, allowing for multiple-story podiums. By allowing two-stories of podium to support five stories of wood framed structure, it maximizes vertical space potential, while using a combination of structural materials to reduce construction costs. As states continue to adopt the International Building Code update, the use of podiums will continue to increase.
Nevertheless, a host of new technologies, techniques, and design capabilities have expanded the podium toolkit beyond the traditional three-bay design of beams, columns and hollowcore plank. Depending upon the needs of the project; owners and designers can tap into the full line of prefabricated building components to get more from their podium designs.
Through the incorporation of double tee precast components, designers can expand the range of their podiums to include multi-level hollowcore plank podiums, multi-level hollowcore plank and double tee podiums or long-clear-span, multi-level double tee podiums.

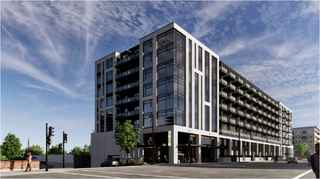

Nova Multi-Family Building - Milwaukee, WI. Learn more here.

Doubling Down on Double Tees in Podiums
Whereas the simple, traditional podium includes short-span prefabricated components consisting of two rows of columns, beams and hollowcore plank through the middle of the structure, double tees can create a clear span across the entire building. That, in turn, maximizes parking areas and eliminates much of the deep foundation expense that would otherwise be needed for columns and beams. As a benefit to the end user, the reduction of columns and beams throughout the parking area creates an open layout with increased visibility to support a sense of security.
It’s not suitable for every application, of course. A designer might gain the benefits of a column-free space beneath a structure, only to sacrifice the load that the system can support. Additionally, double tees could prevent the incorporation of inset balconies or other complex designs at lower floor elevations.
But there are plenty of circumstances where double tees could be the optimal, and most practical, choice. In dense metropolitan areas, the incorporation of double tees is enabling developers to squeeze parking and residential spaces within a small, but expensive, footprint. Elsewhere, areas with poor soil conditions are another ideal setting for double tee use, given the building solution’s ability to minimize foundation work and thereby reduce job costs.
The untapped potential of double tees in podium designs is gaining traction in other market types as well. When Wells is involved in a design-assist capacity early in a project’s life cycle, we’ll always help navigate the best building solution for the project needs.
Author:
Auggy Chung
Wells, Vice President Sales - Great Lakes
Auggy began his career over 25 years ago as an engineering manager and pulls from his experience outside the industry as a real estate preconstruction manager, bringing unique insight to any challenge he encounters. Utilizing his in-depth understanding of the technical, development, and construction side of the business, he provides inventive building solutions for his clients and their communities. Wells is one of the nation’s largest building solutions providers, specializing in prefabricated construction solutions and Auggy leads the sales team for the Great Lake region encompassing Wisconsin and Illinois.