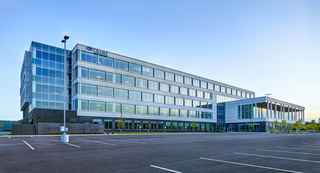

The healthcare community is increasingly turning to prefabricated materials to achieve the dual objectives of efficiency and originality for medical centers and medical office buildings (MOBs). Building owners and administrators are recognizing how prefabrication can streamline the design and construction process, reduce job site clutter, and enhance overall project control. But, when is prefabrication the right construction method?
Challenges of Medical Center Design
For many healthcare projects, decisions must be collaboratively made by teams of doctors, administrators and investors before a project can move forward. This “decision by committee” process can take weeks, if not months, as they explore room sizes, layouts, window locations, and aesthetic and structural requirements. The extensive collaboration ensures that the final design meets the diverse needs of all stakeholders, but it can also delay the project timeline significantly.
On top of that hurdle, it’s a balancing act for the project team – erecting the structure quickly while meeting specific and challenging design objectives like:
- Operational Efficiency: The design must facilitate efficient workflow and operations within the facility. This includes optimizing space for necessary medical equipment and incorporating functional layouts that support specialized medical procedures while minimizing delays and bottlenecks.
- Future Flexibility and Scalability: Healthcare facilities need to accommodate evolving medical practices, technological advancements, and patient needs. A major challenge is designing a space that allows for future expansion or reconfiguration without significant disruptions or renovations.
- Budget Constraints and Cost Management: Balancing high-quality construction with budgetary constraints is no easy task. Costs can quickly escalate due to the specialized nature of healthcare facilities, the need for advanced technology and materials and the longer construction timelines often required for such complex projects.
Other design objectives can involve infection control and regulatory compliance down to extremely minor details. Design teams may need to consider using materials and finishes that are easy to clean and maintain or that work efficiently with their required ventilation systems. Addressing these challenges requires careful planning, coordination and innovative solutions throughout the design and construction process.
How Prefabrication Responds to Healthcare Challenges
Prefabrication is a powerful solution to many challenges faced in healthcare construction. In many cases, prefabricated systems provide an “all of the above” solution, especially when multiple potential future developments exist. One example is Twin City Orthopedics (TCO) facilities across Minnesota. TCO utilizes prefabricated systems to suit its unique needs of speed, functionality and design uniformity. Each new TCO project uses insulated precast panels, designed to the facility’s unique requirements, with an exterior of multi-colored inlaid brick and formliner finishes, windowsill projections, and headpieces cast into the panels, expediting construction and creating a high aesthetic standard across all TCO locations.
To increase manufacturing speeds and provide the best value for TCO, Wells developed a standardized process for easily replicating exterior-facing panels during prefabrication. Even though many of the exterior-facing panels are unique designs, they’re produced in the same dimensions and incorporate standard window sizes and ingredients. Choosing these repeated design elements increases the speed of formwork and casting, enhancing the speed during every step of the process – from design through manufacturing through delivery and installation.
TCO - Waconia, MN
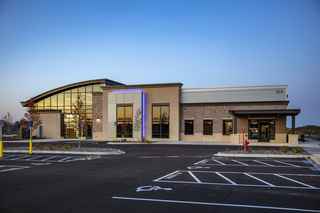

For this facility, Wells produced and installed a building enclosure of architectural and structural load-bearing insulated precast wall panels, with an architectural façade showcasing a mix of replicated stone via a formliner, cast-in thin brick and etched finish elements with varying levels of projecting surfaces, paired with structural panels that are covered in metal to give a very stylish and unique look to the building. Learn more
TCO - Brooklyn Park, MN
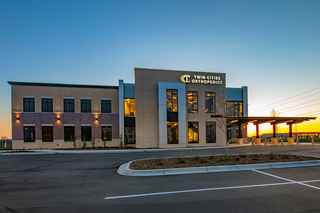

This 37,000 sq ft world-class orthopedic care and rehab center utilizes a blonde-colored mix with formliner at the base and red-tinted flat brick above, with a small cornice projecting out from the design, creating a sense of depth to the structure. The front of the building features a large buff-colored etched architectural precast panel and another smaller panel that is sheathed in a thin metal to contrast the backdrop. The panels also provide lateral support for the building to prevent damage to the structure in the event of strong winds. Learn more
Wheat Ridge Medical Offices
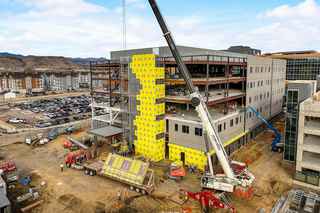

When the design team for a five-story medical office on the Lutheran Hospital campus at Wheat Ridge, CO, was challenged with finding a building envelope solution to meet project goals without requiring structural redesign, they used Infinite Facade™, a unitized building envelope system. The solution avoided serious structural redesign delays on the project and blended the extensive architectural capabilities of a thin, lightweight precast exterior with a steel frame, insulation, and pre-installed glazing, arriving on-site as a complete facade panel. This system immediately enclosed the building and significantly expedited project schedules. For this project, 89 panels were installed in just 9 days, allowing other trades in faster. Learn more
Hudson Medical Center
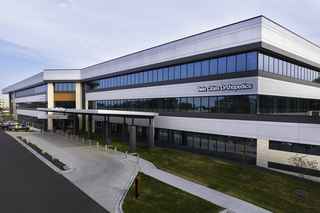

To support future expansion and replacement of large medical equipment needs, Wells designed removable panels in the Hudson Medical Center design. This approach offers significant advantages in terms of flexibility, accessibility, and cost-saving measures for the facility. The total precast building also featured zero-vibration rooms to accommodate MRI machines. Learn more
Prefabrication offers substantial benefits in efficiency, cost management and design flexibility. By utilizing prefabricated systems, healthcare facilities can overcome the challenges posed by their unique design process and specialized use. As the healthcare industry continues to evolve, the adoption of prefabrication techniques is likely to become even more prevalent, driving innovation and enhancing medical facilities function.
Learn more about Wells' healthcare market expertise.