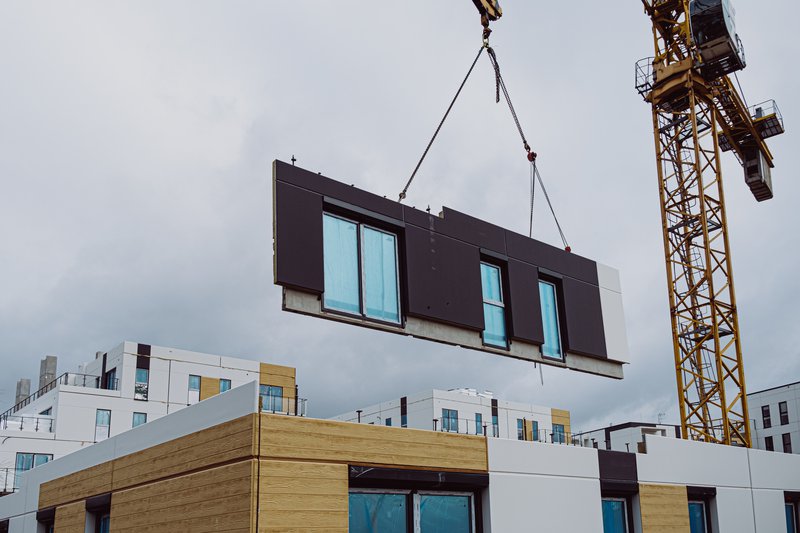
In the world of architecture and construction, innovation is constantly driving changes in how buildings are designed and assembled. One such innovation that has gained significant attention is prefabrication. Prefabrication, also known as modular construction or offsite construction, involves manufacturing building components in a controlled factory environment before transporting them to the construction site for final assembly. This approach offers numerous benefits, including cost savings, time efficiency and improved quality control.
In this guide to prefabricated construction, we will explore the concept of prefabrication, its various methods and components, the benefits it provides, as well as the challenges and considerations involved. We will also discuss its potential as the future of the construction industry and address frequently asked questions about prefabricated construction.
What is prefabrication?
Prefabrication refers to the process of creating building components or modules in a manufacturing setting, away from the construction site. These components can be produced in a variety of customer configurations, using standardized specifications to ensure consistency and precision. Prefabrication offers a systematic and efficient approach to high-end building materials for construction by streamlining the manufacturing and assembly processes.
What is prefabricated construction?
Prefabricated construction is a construction method that utilizes prefabricated components to build structures. It involves the use of factory-made modules, panels or assemblies that are transported to the construction site and assembled into a complete building. This approach is often used in residential, commercial and industrial construction projects, among others.
It's important to note the distinction between prefabrication, modular construction and offsite construction. While all three terms are often used interchangeably, modular construction specifically refers to the use of pre-engineered modules that can be combined to create a variety of building configurations. Additionally, in precast manufacturing, there is a nominal module dimension that is usually 10-foot or 12-foot widths for wall panels and double tees. Offsite construction, on the other hand, encompasses both prefabrication and modular construction, emphasizing the idea of moving construction activities away from the actual site for increased job site safety and efficiency, as well as significant time savings.
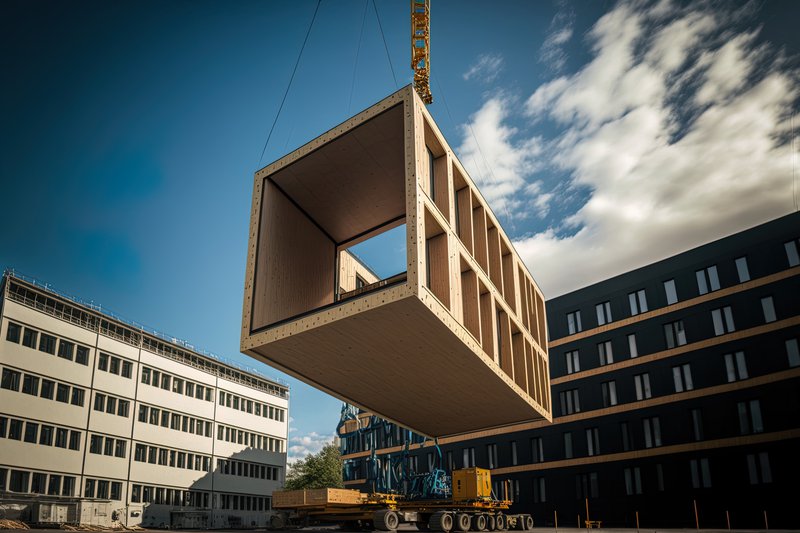
Common terms and concepts in prefabricated construction.
To fully understand prefabricated construction, it's helpful to become familiar with some common terms and concepts associated with this construction method. Here are a few key ones:
- Panels: Prefabricated panels are flat components manufactured offsite, typically made of materials such as wood, steel or concrete. They can be used for walls, floors and roofs.
- Modules: Modules are complete units or sections of a building that are manufactured offsite and transported to the construction site. They can be standalone units or combined to create larger structures.
- Assemblies: Assemblies refer to pre-made components that are joined together to form a specific part of a building, such as trusses or staircases.
- BIM (Building Information Modeling): BIM is a digital version of a building's physical and functional characteristics. It allows for better visualization, coordination and communication during the prefabrication process.
- Just-in-Time Delivery: Just-in-time delivery is a logistics strategy that ensures prefabricated components are delivered to the construction site precisely when they are needed, reducing storage requirements and minimizing delays.
- Integrated Project Delivery (IPD): IPD is a collaborative and mutually beneficial approach that involves all stakeholders, including designers, contractors and manufacturers, working together from the early stages of a project to optimize efficiency and achieve project goals.
Prefabricated components.
Prefabricated construction relies on a range of components that are manufactured offsite and then transported to the construction site for assembly. Let's take a closer look at some commonly used components:
- Wall Panels: Prefabricated wall panels are produced with insulation, sheathing and other necessary components. They can be customized with various finishes and designs.
- Double Tees: Double Tees are pre-engineered structural frameworks that support the roof. They are manufactured with precision and can be quickly installed on-site.
- Pods: Pods are prebuilt modules that are completely constructed off-site. Bathroom pods for example are complete bathroom units that are manufactured offsite, including plumbing fixtures, electrical wiring, and finishes. They can be easily integrated into the building structure.
- Floor Cassettes: Floor cassettes are prefabricated floor units that include structural elements, insulation and finishes. They can be manufactured with openings for easy installation of services.
These are just a few examples of prefabricated components commonly used in construction. In terms of precast, additional prefabricated components include columns and beams, stairs and stadia and spandrels. The use of these components helps accelerate the construction process and ensures higher quality control.
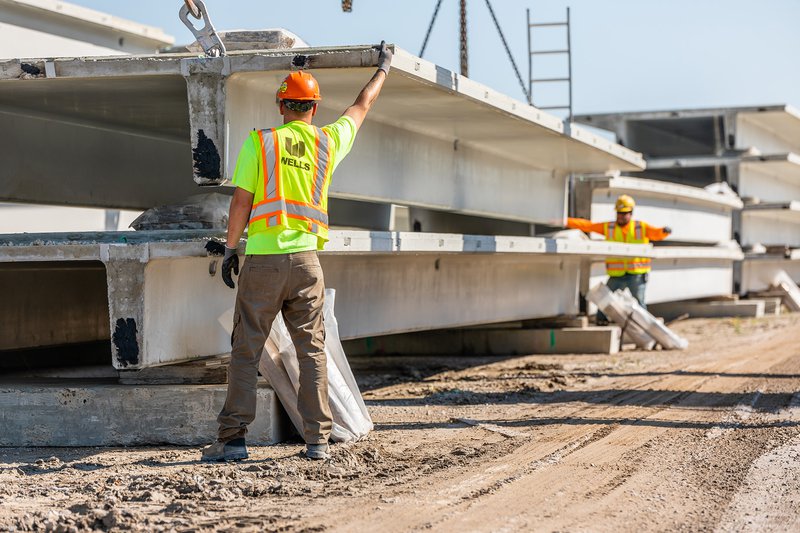
Prefabricated construction methods.
Prefabrication can be achieved using different construction methods. A few include:
- Volumetric Construction: Volumetric construction involves producing entire modular units, often referred to as modules, in a factory. These modules are then transported to the site and assembled into a complete building.
- Panelized Construction: Panelized construction focuses on the fabrication of individual panels, such as wall panels, floor panels and roof panels. These panels are transported to the site and assembled on-site to form the building structure.
- Hybrid Construction: Hybrid construction combines both on-site construction and prefabricated components. Certain parts of the building may be constructed traditionally on-site, while other components, like walls or modules, are prefabricated and assembled offsite.
The choice of construction method depends on project requirements, budget, timeline and the desired level of customization.
Benefits of prefabricated construction.
Prefabricated construction offers several advantages over traditional on-site construction methods. One significant advantage of prefabrication is cost savings. By standardizing the manufacturing process, materials can be efficiently used, and economies of scale can be achieved. Additionally, the ability to reuse plans and materials across multiple projects helps reduce costs and waste.
Another benefit of prefabrication is the significant reduction in construction time. Since components are manufactured offsite, the construction process can proceed simultaneously on the site while modules or panels are being fabricated. This parallel work reduces project timelines and accelerates project completion.
Prefabricated construction allows for rigorous quality control measures. Since components are manufactured in a controlled factory setting, builders can closely monitor and inspect each component before it is delivered to the construction site. This results in a higher level of quality assurance and consistency. These benefits make prefabricated construction an attractive choice for many projects.
Challenges of prefabricated construction.
While prefabrication offers numerous advantages, there are also some challenges that need to be considered. Addressing these challenges requires proactive planning and effective communication among all project stakeholders.
- Prefabrication can impose certain design limitations compared to traditional construction. The modular nature of prefabricated components may require specific design constraints to ensure structural integrity and ease of transportation. However, advancements in technology and design capabilities are continually expanding the range of possibilities for prefabricated construction.
- Transporting large, prefabricated components to the construction site requires careful planning and coordination. Challenges related to logistics, such as obtaining necessary permits, ensuring proper handling during transportation, and coordinating delivery schedules, need to be effectively managed.
- Proper site preparation is crucial for successful prefabricated construction. The construction site needs to be adequately prepared to accommodate the arrival and installation of prefabricated components. Close coordination between offsite and on-site work is essential to ensure a seamless integration of the prefabricated components into the overall construction process.
Key considerations for implementing prefabricated construction.
Implementing prefabricated construction requires careful consideration of several factors. Not all projects are ideally suited for prefabricated construction. Assessing the project's complexity, size and design requirements is crucial in determining whether prefabrication is a suitable approach. Certain projects, such as multi-story buildings or projects with unique architectural designs, may require a hybrid approach that combines prefabricated components with traditional construction methods.
Successful implementation of prefabricated construction relies on effective collaboration and communication among all project stakeholders. Architects, engineers, manufacturers, contractors and suppliers need to work together closely from the early stages of the project to ensure seamless integration of prefabricated components into the overall construction process.
It is essential to understand the building codes and regulations specific to prefabricated construction. Different regions may have varying requirements and compliance standards. Ensuring compliance with these codes and regulations is vital for a successful and legally compliant construction project.
Are prefabricated structures the future of construction?
Prefabrication is gaining increasing popularity in the construction industry, and many companies, like Wells, are embracing this innovative method. The benefits of cost savings, time efficiency and improved quality control make prefabrication an attractive option for both builders and clients.
Moreover, prefabricated construction aligns with the growing emphasis on sustainability and energy efficiency in the industry. The controlled factory environment allows for better waste management, material optimization and integration of eco-friendly technologies. As the construction industry continues to evolve, prefabricated construction is likely to play a significant role in shaping its future.
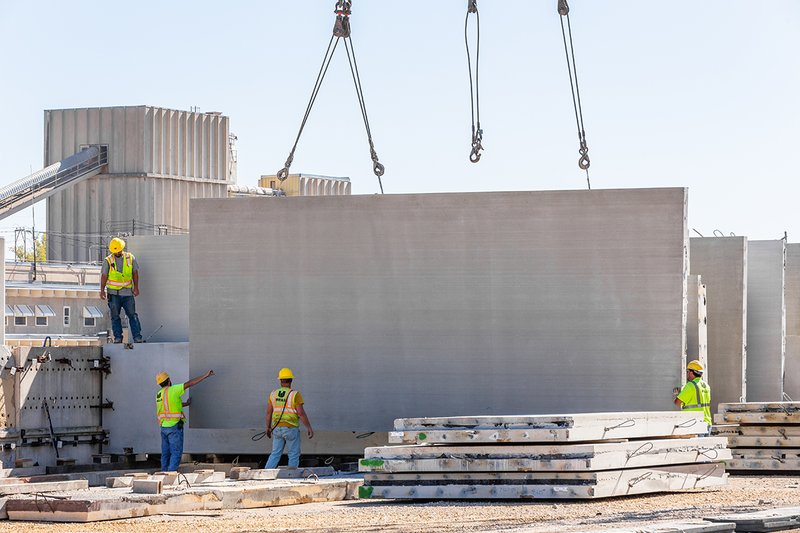
Prefabricated construction FAQs.
Q: Are prefabricated buildings customizable in terms of design and layout?
A: Yes, prefabricated buildings can be customized in terms of design and layout. While there may be certain design constraints to ensure structural integrity and transportation feasibility, prefabrication techniques can accommodate a wide range of design options and customization.
Q: How is the quality of prefabricated components ensured?
A: Prefabricated components undergo rigorous quality control measures throughout the manufacturing process. These include thorough inspections, adherence to industry standards and regulations and quality assurance protocols implemented by the manufacturers. Additionally, certifications and third-party inspections can provide further assurance of quality.
Q: How does prefabricated construction contribute to faster project timelines?
A: Prefabricated construction significantly reduces project timelines by allowing for parallel work. While site preparation and foundation construction take place, prefabricated components are manufactured offsite. This concurrent activity saves time compared to traditional sequential construction methods.
Q: What cost savings can be expected with prefabricated construction?
A: Prefabricated construction offers cost savings through multiple avenues. Standardization and efficient manufacturing processes lead to material and labor cost savings. The reuse of plans and materials across multiple projects reduces waste and optimizes resource utilization.
Q: What is the lifespan and durability of prefabricated buildings?
A: Prefabricated buildings have a lifespan and durability similar to traditionally constructed buildings. The quality of materials, adherence to construction standards and regular maintenance play vital roles in ensuring the longevity of prefabricated structures. With proper care, they can provide long-lasting and durable solutions.
Q: Are there any specific building codes or regulations for prefabricated construction?
A: Building codes and regulations for prefabricated construction may vary by region or jurisdiction. It is essential to consult local building authorities to understand the specific requirements and compliance standards for prefabricated construction projects.
Q: Can prefabricated construction be combined with traditional construction methods?
A: Yes, prefabricated construction can be combined with traditional construction methods. Hybrid construction approaches leverage the benefits of both methods to achieve desired results. For example, prefabricated components can be used for certain building elements, while on-site construction is employed for other parts of the structure.
Q: How do I get started with a prefabricated construction project?
A: To get started with a prefabricated construction project, follow these steps:
- Define your project goals and requirements.
- Assess the project's suitability for prefabrication by engaging with architects, engineers, and manufacturers experienced in prefabricated construction.
- Collaborate closely with all stakeholders to develop a comprehensive project plan.
- Ensure compliance with building codes and regulations specific to prefabricated construction.
- Establish a clear timeline, logistics plan and budget for the project.
- Monitor the manufacturing and transportation processes to ensure quality control.
- Coordinate site readiness and integration of prefabricated components with on-site construction activities.
- Regularly communicate and address any challenges or concerns that arise during the project.
- Conduct thorough inspections and quality checks throughout the construction process.
Prefabricated construction offers numerous benefits versus traditional construction methods, including cost savings, time efficiency and improved quality control, and has the potential to shape the future of the construction industry. By embracing this innovative method, builders can deliver projects more efficiently while meeting the evolving demands of sustainability and energy efficiency.