What is hollowcore?
Hollowcore gets its name from large cast voids in the section during the manufacturing process. The large voids in hollowcore are used to reduce the weight of the system and increase spans. Prestressing steel is included in the section to further increase the span-to-depth ratio and increase the load-bearing capacity of the individual members. Hollowcore properties, often make it an economical solution for floor systems.
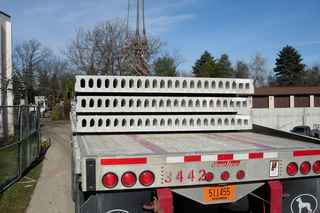
Hollowcore in construction.
Hollowcore slabs can be finished in various ways to suit structural load requirements. If a field topping is not needed, the keyways between the individual hollowcore elements can be grouted to facilitate horizontal shear transfer. When a topping slab is specified in the design, the surface of the hollowcore can have a raked finish to enable composite action and horizontal shear transfer.
Due to the inherent voids in hollowcore production, the system design includes built-in redundancy. If additional openings are needed on-site, it is often possible to grout the hollowcore cells around the new openings to accommodate them.
In terms of aesthetics, structural hollowcore can be left exposed or painted for a cost-effective alternative to drywall installation on ceilings.
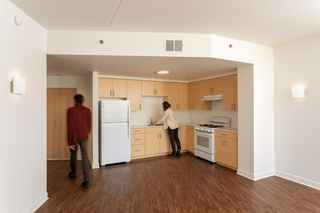
Ideal Project Types for Hollowcore
Offices

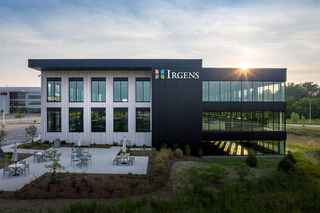
Warehouses/Manufacturing Facilities

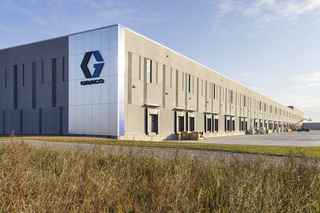
Schools

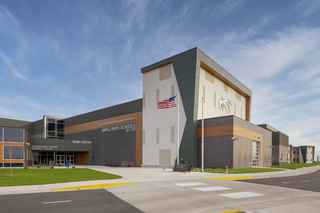
Multi-Family

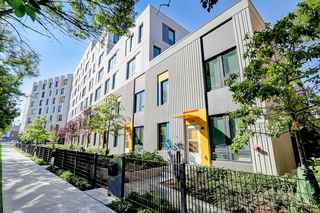
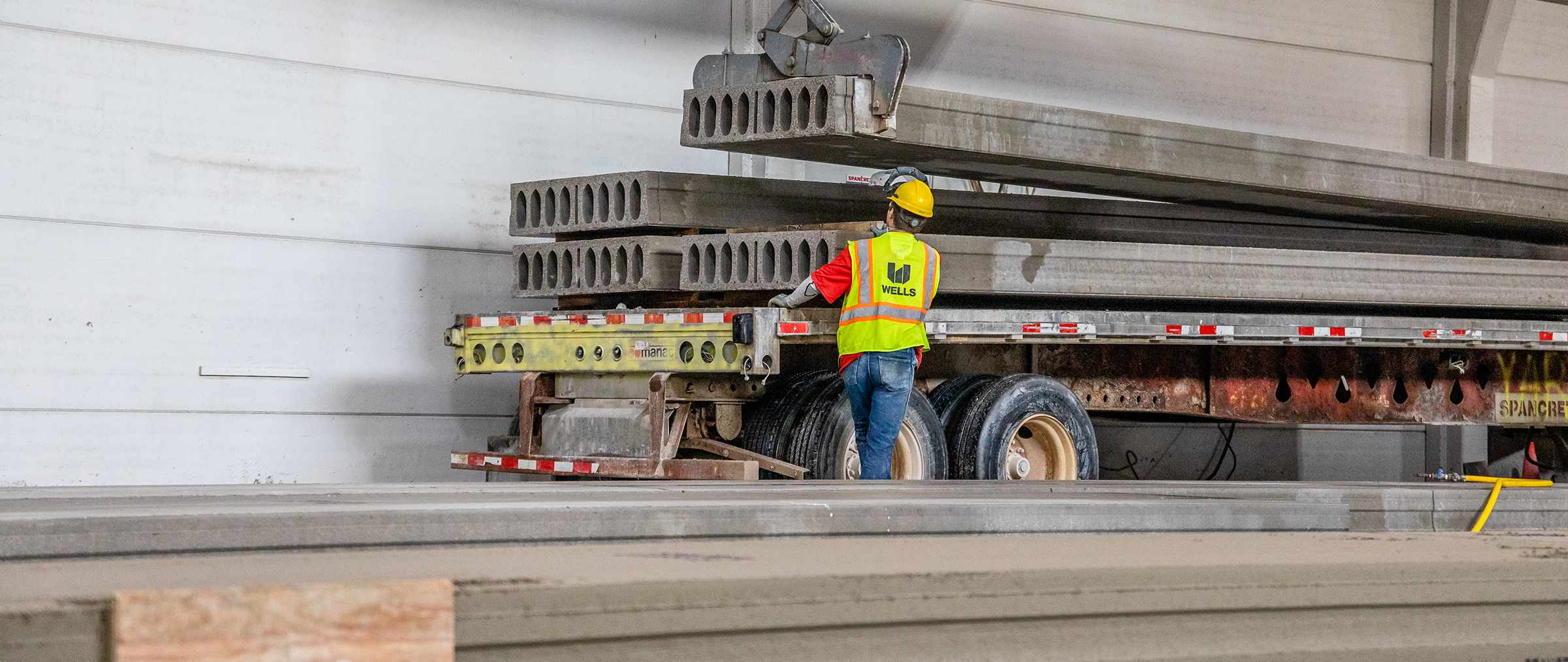
Structural benefits of precast hollowcore.
- Quick installation
- Extremely efficient section
- Lightweight
- Ability to dual purpose as floor and ceiling
Achieving fire resistance goals with hollowcore.
Hollowcore fire resistance varies based on the specified cross-section because fire rating is determined based on the net cross-section area. Typically a 1-hour fire rating can be achieved with no structural topping slab. However, this can easily be increased by grouting additional cores, adding a topping slab, or increasing the depth of the hollowcore as needed.