Durable, efficient precast wall panels.
Precast walls come in a variety of shapes, sizes and dimensions for various building applications, ensuring versatile and efficient building solutions. There are two main types of wall panels: solid precast walls and insulated precast walls, each offering distinct benefits and uses.
What is a solid precast wall panel?
Solid wall panels are poured with continuous concrete throughout rather than including a layer of insulation within the section. Solid panels can be manufactured to be structural, architectural, or both, depending on the desired application. They are efficient structural elements when buildings are not required to be insulated from the weather. Solid walls can also be used as a fire barrier between structures with the ability to achieve a wide array of fire ratings depending on the final panel thickness.
What is an insulated precast wall panel?
Unlike precast solid wall panels, insulated precast wall panels include rigid insulation incorporated into the wall cross-section. The insulation can be attached to the concrete panels to achieve either non-composite or composite behavior, enhancing the structural performance of the wall cross-section. Similar to solid wall panels, insulated wall panels can be designed for structural, architectural, or combined purposes, depending on the desired application.
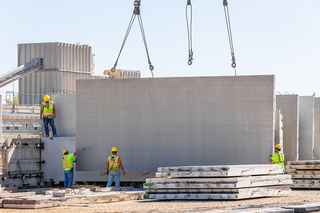

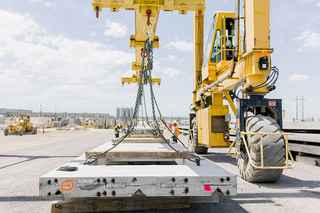

Determining insulation thickness for r-value.
The insulation thickness can be adjusted to increase or decrease the desired thermal insulating property. The concrete surrounding the insulation can also be increased or decreased depending on the structural demand on the walls. Typical insulated wall panel cross-sections of concrete to insulation to concrete are 6-3-3, 6-4-3, 3-3-6, 4-3-3, and 4-4-4. The Wells preconstruction and engineering team can provide guidance on adjustments to achieve the desired thermal properties or structural demand.
Ideal Project Types for Prefabricated Wall Panels
Solid Wall Panels
Parking Garages

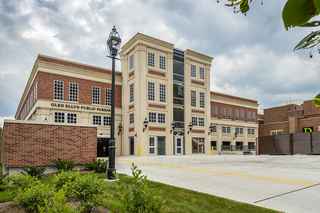
Interior Walls

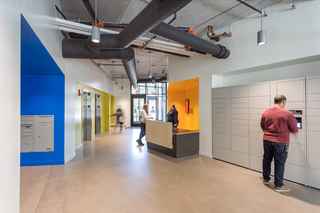

Insulated Wall Panels
Schools - Higher Education & K12

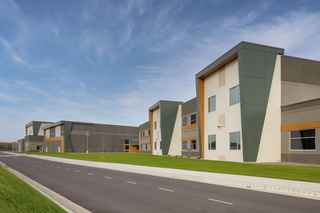
Industrial

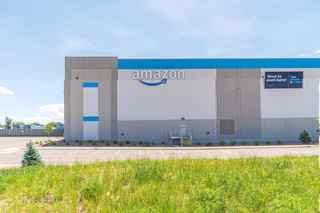
Offices

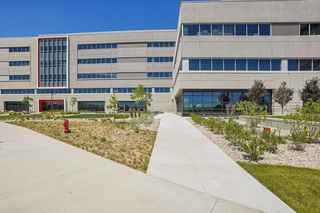
Design Tips for Prefabricated Wall Panels
Load-bearing vs. non-load-bearing wall panels.
Wall panels can be load-bearing, supporting the structure's framing, or non-load-bearing, which does not support any of the building's structural framing. Shear walls transfer lateral forces from the superstructure to the foundations, acting as cantilevered elements to collect loads from wind or seismic events. Depending on their placement, these walls can also eliminate the need for other structural gravity elements, such as columns, and reduce beam sizes.
Engineering prefabricated openings to save time in the field.
With preconstruction coordination, our walls often incorporate cast-in electrical during the manufacturing process, allowing for less on-site work, along with coordinated penetrations in the wall panels to minimize the amount of on-site coring required.
Achieving desired aesthetics.
If architectural solid walls are desired, there is a multitude of finishes and architectural surfaces that can be achieved. Depending on the depth of the architectural surface the thickness of the walls can also be adjusted to accommodate the structural demand on the panels.
Manufacturing wall panels in a quality-controlled environment.
Our walls are poured horizontally with the exposed or architectural face down on customized steel forms. The back face of the wall, also known as the screed face, can be left exposed in the final design with varying finishes depending on specifications. From a float finish to a hard trowel to produce a wall with minimal variations.
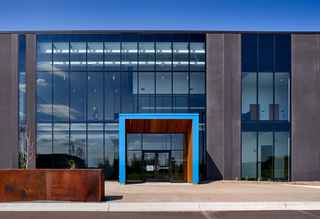

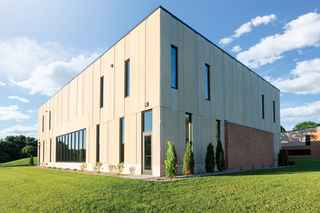

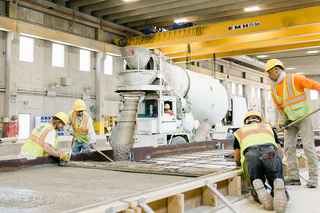
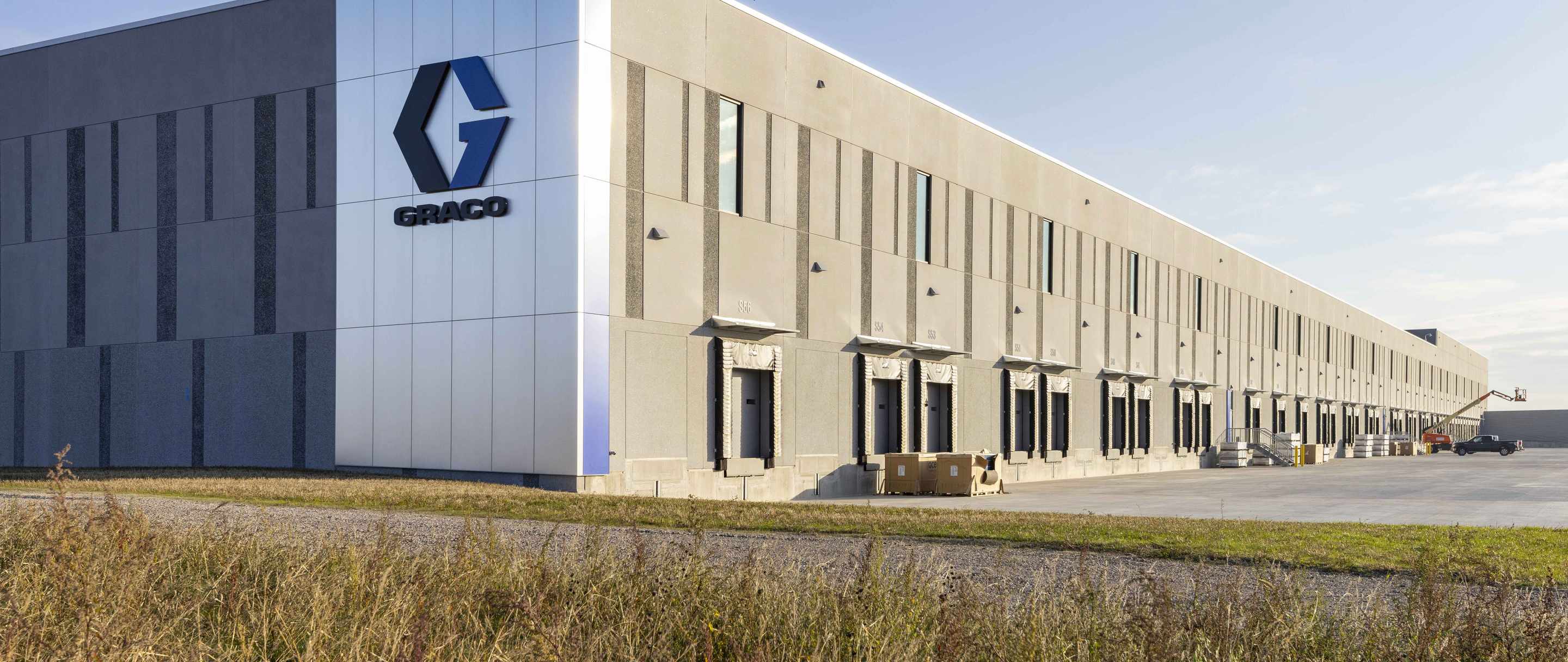
Structural benefits of precast wall panels.
- Cross-section flexibility - openings can be added as needed without impacting the structural design
- Fire resistance
- Lateral design efficiency
- Thermal efficiency, especially in insulated wall panels
- Flexibility to accommodate future openings or expansion