Epitomizing a true sense of community.
The city and county of Broomfield, Colorado, epitomizes a true sense of community - unifying its residents, guests, and visitors. For the suburb of Denver, having one centralized building to connect its diverse population was an essential goal for a new community center. A complex, multi-phased demolition and full rebuild of what was an aging and deteriorating recreation and senior center was critical to providing an expansive, updated facility. The owner’s overarching goal was to create a landmark that would connect not only the physical building and lush open space to its existing city campus, but that was inclusive and welcoming to all generations in the community.
Unique to this project, a design build solution incorporating precast concrete was selected for the Recreation Center half of the facility. The Recreation Center specifically required a building material that provided durability, flexibility, efficiency, safety, and a façade to blend with the city and county’s color and material pallet. Although a tall order, precast concrete was identified as the ideal and most efficient solution. Acknowledging the wide variety of amenities this center would make available to its guests; intense planning, maximized coordination and over-the-top attention to detail were essential to build a 60,000 plus square foot building with an accelerated construction schedule.
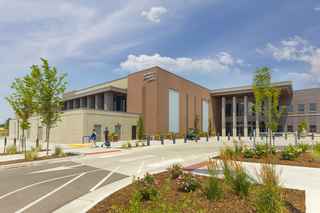

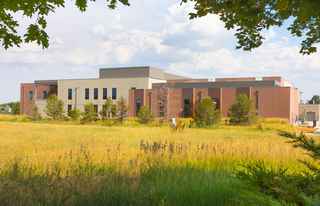
It's all in the details.
Essential to complementing the city and county’s color pallet, materials and textures, the team painstakingly worked to create specialized surfaces and custom architectural mixes. The exterior of the natatorium and fitness center includes a Reckli - Columbia, wave-like form liner that hints at the interior aquatic space’s use. Another goal was to drive indirect sunlight into and through the warm pool and a sawtooth façade on the north elevation was the perfect feature. A custom, ribbed liner was used sparingly as an accent at the main entry and around the natatorium that picked-up the masonry detailing on the adjacent senior center. In this application and to ensure color consistency on the façade, acid etching was used on all of the architectural, precast concrete.

In our world of increasing extreme weather events, precast concrete will always give your project a predictable outcome.
Room for activities.
The vision was an open, true community and welcoming character, with great long span volumes for the community to gather. To bring this vision to life, the project team leaned on precast concrete to drive the design. Unique to this structure, our team produced five different depths of double tee’s, ranging from 40’-0” to 109’-0” in length, utilized as roofing and floor members. A well thought out and engineered solution allowed for a composition of varying roof heights from the natatorium to fitness center to gymnasium which developed into the quickest, safest, and most efficient result.
The high volume created by the long-span precast concrete double tees and insulated, precast concrete walls in the multi-use gymnasium provided an additional benefit – this allowed integration of a Level 2, cantilevered, three-lane running track off the walls. This also created a looped viewing platform for the athletic activities on ground level.

Weathering the storm.
Utilizing a total precast solution allowed for key challenges to be minimized from the start, including unknown weather delays. With erection taking place in the brunt of Colorado’s extreme and uncertain winter, the team prepared accordingly. Although, no one would anticipate the unprecedented historic Bomb Cyclone and vicious winds, the project team successfully managed weather impacts with thoughtful site management and logistics.
The unpredictability of Colorado’s winter weather played a starring role during the precast structural and façade erection. A trifecta of wind, below freezing temperatures and accumulating snow, and the 2019 Bomb Cyclone inevitably caused havoc. Ninety miles per hour winds and heightened safety concerns caused a three-day project halt. However, precast concrete is produced off site, production continued in the plant which allowed for advanced planning and preparation for rapid product delivery to the site when the historic storm had passed. Once conditions on site were deemed safe, building components arrived just-in-time, playing an important role in allowing the project to quickly get back on track and eliminated additional schedule delays and other on-site conflicts.
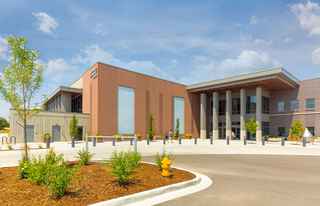

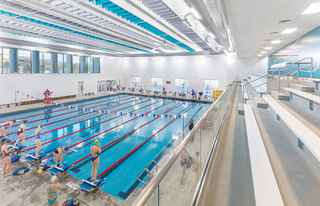
Innovations benefiting the future.
Not only was precast concrete utilized to construct the core and shell of the building it also contributed to the mitigation of the site’s highly expansive soils at the locker rooms. Excavation of an additional 6 feet created a crawl space that was topped with 40” deep precast concrete double tee flooring. The heated area allowed for suspended, sloping plumbing, which let the soil naturally expand and not impact utilities. Precast eliminated the complex option of direct burying utilities, which in turn prevents future disruption and protects the hanging piping while providing convenient access for maintenance and repairs.
With direction to design and build an energy efficient structure that exceeded ASHRAE 90.1 and International Energy Conservation Code requirements, insulated wall panels were used that had an R-Value of 17.4. Precast concrete insulated wall panels do not contain voids or cavities where moisture can collect, in the inherently high humidity natatorium spaces, mold and mildew growth are no longer a concern. The insulated precast concrete wall panels were reinforced with a carbon fiber grid system called C-GRID®. The C-GRID® system allowed for thinner precast sections and reduced the weight of the enclosure system and foundation sizing while significantly improving the insulation value of the walls. In addition, the mass of the gymnasium and fitness center’s walls help control sound transmission into the adjacent Senior Center.
This project was featured in the PCI ASCENT Fall 2022 edition - read now.
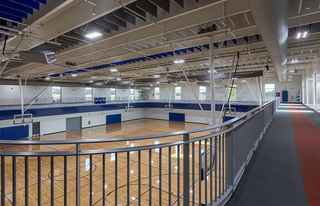
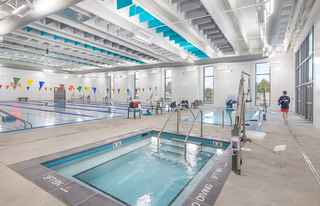