Creating space to elevate communities.
Located behind the existing historic Civic Center on what used to be a small parking lot, the Public Parking Garage provides 277 additional parking stalls to the downtown district on otherwise non-developable property. The structure is 5 precast levels, including a lower (basement) level.
From the onset of the project, the Village set the expectation that their new parking structure must not only complement the historic downtown district, but also be economical from the construction costs and maintenance costs viewpoints.
PCI's 2022 Design Award for Best All-Precast Concrete Parking Structure
Thoughtful expansion in a historic location.
In the early phases of the design process, the design-build team analyzed the benefits and shortcomings of both precast concrete construction and cast-in-place post-tensioned concrete construction for the Village. This process included developing schematic level documents of both structural systems, and then producing an in-depth life cycle cost analysis for the village to use as a tool for selecting the ideal construction type.
Construction constraints were a major factor influencing the selection of the structural system. Although this structure is located in a suburban Village, the unique site proved to rival the maximization of real estate that is typically reserved for urban downtown construction. Essentially, this garage required nearly zero-lot-line construction on the vast majority of the perimeter of the garage. As the crane and trucks only had a single access point, the benefit of precast requiring little to no onsite storage played a key role in logistics and planning.
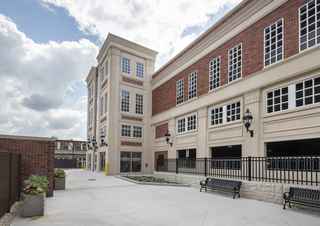
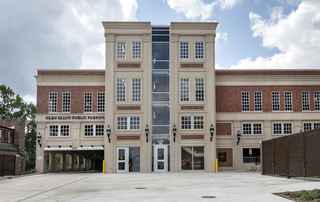
All-weather construction capability.
The garage’s neighbors included residential dwellings, restaurants, hair salons, government buildings, and even dance studios. The design-build contractor identified from the early design drawings that the use of precast would not only expedite the construction schedule, but also would be the least disruptive to the neighborhood residents and visitors when accounting for the site constraints. Utilizing the prefabricated precast building components was a significant benefit to the Village, as concrete quality and casting conditions can be optimized, then bringing the precast pieces onto the project site in phases to be quickly swung into place.
Due to a large portion of the construction schedule happening in cold weather, utilizing a different building material would have negatively impacted the schedule when compared to precast. However, precast has all weather construction capability and therefore erection did not require temperature cold-weather concreting provisions such as heaters and frost blankets, whereas other building materials would have.
Driving design items.
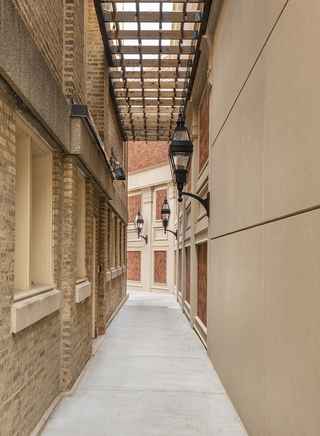
With the requirement to provide a high-end façade for the garage to pay homage to the surrounding historic architecture and to blend the garage into the downtown district, an architectural precast cladding, regardless of the construction type, was identified as one of the driving design items for the garage. If a post tensioned system was utilized, any architectural precast façade would simply be cladding, whereas with precast construction, the architectural precast wall panels could serve double duty as both the façade and the bearing wall system. This ability to provide one piece of precast for both function and facade gave precast the edge over cast-in-place post-tensioned construction.
The architectural precast wall panels with thin-set brick and dramatic cornices were designed to be similar to the architecture of the historic Civic Center. Thin-set brick was utilized in multiple patterns on the different wall panel type, which included running bond and basket weave. The thin brick and intricate coping details were added onto each piece of precast, eliminating the need for additional trades, building components, and connection details. The surrounding precast concrete mix design that framed the thin brick sections was optimized to mimic the original local limestone that the adjacent historic building featured.
“Precast concrete lent itself really well to this project to help address all of these issues... It met the budget and schedule and everyone is extremely happy with the result.”
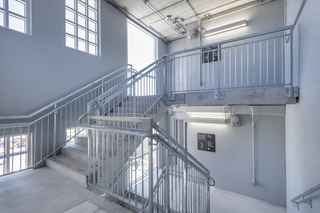

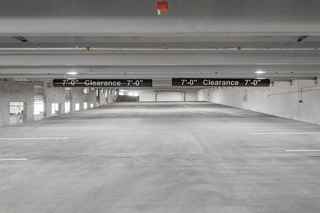
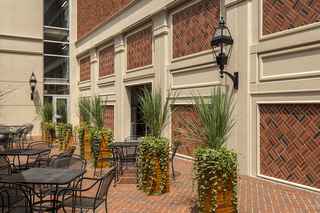
On the interior of the structure, 15’-0” precast double tees were utilized to minimize the number of pieces required to be delivered to the construction site. These double tees spanned between the architectural precast wall panels and the internal vertical ramp walls. At end turning bays, long-span inverted tee beams provided clear unobstructed sightlines for two-way turning movements and end-bay parking.
Once the life cycle cost analysis proved that for this unique site precast construction would be an overall cost savings over cast-in-place, in tandem with the accelerated construction schedule, and limiting the disruption of the neighborhood during construction, precast was the best solution for this beautiful public parking garage.
This project was featured in the PCI ASCENT Spring 2022 edition - read now.