Advanced healthcare under one roof.
This Twin Cities Orthopedics (TCO) building is the first in their network to be fully equipped with all necessary facilities, including an on-site MRI, eliminating the need to refer patients to other locations for advanced procedures. It is also the first TCO facility with three stories, making it a significant step forward in both design and functionality.
The building showcases an innovative mix of materials—brick, stone, precast, and metallic stain—all seamlessly integrated into a unified design. While TCO locations usually follow a consistent exterior facade, the design team always tries to do something creative with each new building. This project was particularly unique because the typical dark metal band seen at the tops of other TCO buildings was largely replaced by more cost-effective prefabricated panels, which were stained to match the metal used in other designs.
MN RE Journal 2024 Commercial Real Estate Award: Medical Property - West
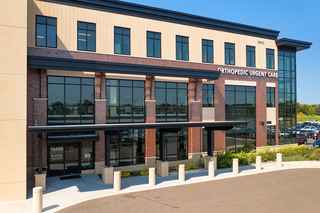

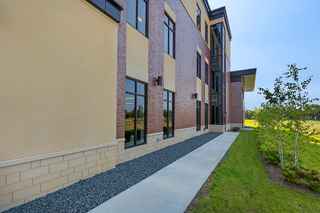
The structure includes a load-bearing precast system, which has been refined through experience. This is the design team’s fifth TCO project, and their growing familiarity with the possibilities of prefabricated systems allowed them to incorporate more advanced details, expanding the building’s aesthetic options. The owners appreciated this continued innovation, making the completion of this project a noteworthy achievement for all involved.
One of the key challenges in this project was coordinating the precast panels with the steel structure. Unlike typical designs where precast panels bear on footings, these panels were supported by steel, which can deflect or shift under load. To address this, the team required extra coordination, working closely with engineers to ensure joint alignment and manage erection tolerances, minimizing any potential disruption. Additionally, the unique layout of the rooms and the steel structure required some irregularly shaped precast panels. Thanks to the flexibility and problem-solving capabilities of the precast team, who like to think of this particular project as a “precast puzzle”, these complexities were successfully navigated.
Early involvement of Wells allowed the design team to fully optimize the building envelope system that we provided. With each successive TCO project, the team was able to push design boundaries while controlling costs, ultimately delivering more value. It’s rewarding for Wells to see how much can be achieved when collaborating closely to bring the client’s vision to life.
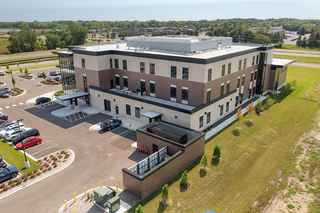

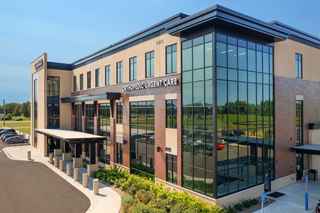