Twin Cities Orthopedics (TCO) in Oak Park Heights, MN, is a remarkable medical office building that expands the family of TCO locations across the greater Twin Cities area. The facility offers world-class orthopedic care, rehabilitation, athletic training, walk-in orthopedic urgent care and physical therapy.
This two-story structure stands as a testament to the fusion of architecture and prefabrication. The building showcases intricate detailing, diverse dimensions, and a variety of finishes, creating a dynamic and visually captivating exterior. The Oak Park Heights location embodies the advantages of prefabrication through speed of construction, aesthetics, and durability.
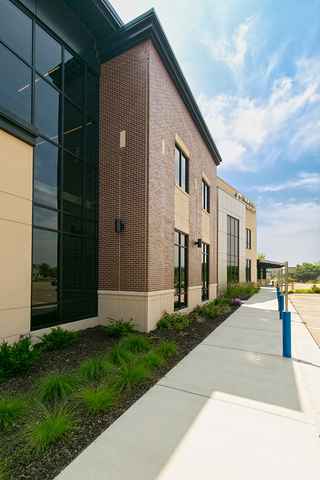
From various angles, recesses, and projections to the striking stacked bond pattern on the columns, this precast building defies expectations. Its captivating aesthetics are a testament to the versatility and artistic possibilities achievable with prefabricated solutions. The exterior of the building combines multiple unique finish techniques to create the appearance of a multitude of different building materials. The facade was created using a formliner to mimic a textured stone effect, providing an elevated exterior appearance. The design employs a combination of finishes on a single panel, using acid etching while also incorporating thin brick in two different colors to provide visual interest and dimension. The panel forms come together to develop the overall building effect, creating a seamless and custom look by incorporating various elements like window openings, and even arched sections, to create a harmonious look.
The success of the development can be attributed to the collaborative approach between the project design and construction partners. By carefully listening to the needs and desires of Sperides Reiners Architects, the architect, Wells was able to deliver the desired outcomes. The prefabrication team's willingness to try new techniques, further enhanced the collaborative process and outcome. This project serves as a testament to the benefits of maintaining a consistent team across multiple TCO projects, fostering an understanding of the client drivers and preferences and strong communication between partners.
For the architectural façade, the utilization of precast panels offered multiple advantages for the structure. The panels accelerated the construction timeline, saving valuable time for project stakeholders, and helping the client gain access to the building to start seeing patients. The precast panels also provided the appearance of a meticulously hand-laid brick building, adding a touch of sophistication to the overall aesthetic.
The project presented several challenges, particularly in terms of intricate detailing and complex panel configurations. The Wells preconstruction team rose to the occasion, embracing challenges to support the design vision.. Notably, the full columns of the building required a build-up approach, integrating brick returns onto the panels. Furthermore, the steel structure was already in place, allowing for a seamless integration of prefabricated elements. The alignment of multiple planes across the precast components demanded meticulous manufacturing precision and attention to detail, with regular and detailed quality reviews to ensure a cohesive and visually stunning result.
For prospective clients seeking architectural excellence, expedited construction timelines, and cost-effective solutions, Twin Cities Orthopedics Oak Park Heights serves as a compelling example. TCO boasts high-end elements, angles, and finishes that rival conventionally built structures. The combination of aesthetics, durability, time and cost savings make prefabricated solutions an attractive choice for healthcare clients that desire outstanding architectural outcomes.
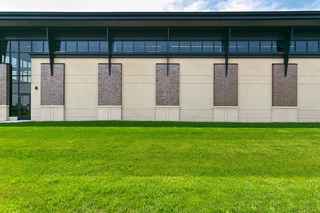
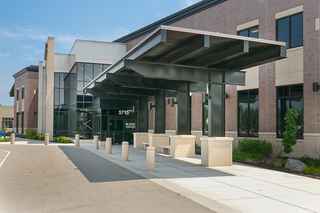
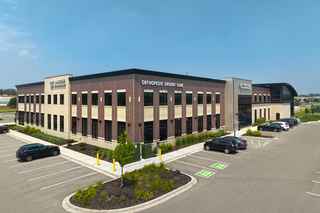